Project Description
Key information
Project title: Driving green innovation: Bosch partners with M2i for Electrolyser Research
Project in the Spotlight: T24010
Funding: This project is co-funded by ‘Holland High Tech, topsector High Tech Systems and Materials’, with a ‘PPS Innovation Grant Public-Private Partnerships for research and development’
Run time: 2025-2027
Market: Circularity/sustainability
Written by M2i Program Manager: Franz Bormann
Hydrogen electrolysis
In the transition to a sustainable energy future, many technologies turn towards hydrogen as the green energy carrier of the future. Electrolysers, which split water into hydrogen and oxygen using electricity, are at the heart of this transformation. They provide a clean, renewable method of hydrogen production that supports decarbonisation across energy and industrial sectors.
Before implementation at scale, several technical and economic challenges have to be solved. These include optimising manufacturing processes, addressing material limitations, and ensuring long-term reliability under harsh operating conditions. The materials used in these electrolysers are subject to severe conditions due to the required environmental conditions to produce hydrogen. As such, the used bipolar plates and sealing systems must meet stringent performance requirements to enable reliable and cost-effective hydrogen production.
To tackle these challenges, Bosch Transmission Technology, in collaboration with University of Twente and TU Delft, is leading cutting-edge research innovations. These efforts, structured around the OptBPP, CorBPP, and OPESED projects, aim to push the boundaries of electrolyser technology. By improving efficiency, durability, and scalability, these projects are paving the way for the widespread adoption of sustainable hydrogen production systems, helping drive the global energy transition forward.
Research Challenges
CorBPP: Corrosion in Bipolar Plates
Corrosion poses a significant challenge in electrolyser technology, particularly for bipolar plates operating in harsh chemical environments characterised by low pH, high potentials, and aggressive ion exposure. These conditions lead to degradation of traditional materials, such as titanium, which can result in reduced efficiency, higher operational costs, and shorter lifespans for electrolyser stacks.
Within the CorBPP project, advanced materials and surface treatments will be explored to enhance corrosion resistance while maintaining high conductivity. Potential alternatives to expensive coatings like platinum and gold include, innovative dopings, and advanced polymer composites. These solutions aim to reduce material costs without compromising durability or performance.
In addition to material development, the project employs sophisticated testing methodologies, including electrochemical and advanced surface characterisation techniques, to investigate the corrosion mechanisms at play. Insights gained are used to develop coatings and surface treatments that mitigate degradation under extreme conditions. These efforts contribute to a new generation of more cost-effective, durable, and sustainable bipolar plates, ensuring their reliability in long-term operation while reducing the overall costs of hydrogen production systems.
OptBPP: Optimal design and manufacturing methodology of electrolyser bi-polar plates
Bipolar plates are critical components in electrolysers, facilitating water and gas transport, ensuring efficient electron conduction, and maintaining the stack’s structural integrity. However, their manufacturing involves significant challenges, including the complex geometries required for optimal performance, and the demanding mechanical and chemical conditions under which they operate.
To address these issues, the OptBPP project first focuses on developing enhanced material models that accurately predict the titanium behaviour during thin metal forming. These models account for titanium’s anisotropic mechanical properties, tension-compression asymmetry, rate dependence, as well as damage. The enhanced material models are then integrated into an advanced numerical tool for virtual prototyping. This tool simulates the production of titanium bipolar plates, reducing reliance on expensive physical prototyping and minimising material waste. By enabling precise optimisation of design parameters, tooling configurations, and processing conditions, a more efficient and reliable manufacturing workflow will be enabled.
OPESED: Optimal eleyctrolyser sealing design
Sealing components play a vital role in the efficiency and safety of electrolyser stacks, ensuring the containment of water, electrolytes, and gases under high-pressure and high-temperature conditions. However, achieving reliable and long-lasting seals is a challenge due to the impact of surface roughness, material degradation, and the formation of microscopic pathways that lead to leakage over time – the so-called percolation channels.
In the OPESED project, a dual approach combining experimental studies and numerical modelling will be implemented. On the experimental side, the seal surface roughness will be characterised to quantify roughness profiles across multiple length scales. These measurements provide critical input for numerical models and establish benchmarks for material specifications.
On the numerical side, a multi-scale approach will be employed. At the component scale, FEM models analyse contact areas and nominal pressures influenced by component geometry, applied loads, and material properties. These outputs feed into smaller-scale models that simulate the formation of percolation channels. The Boundary Element Method (BEM), coupled with thin-film flow models, will be used to predict leakage rates based on surface topology and mechanical properties.
Once validated through experimental data, the combined models will be used to develop design guidelines for sealing components. These guidelines will optimise material selection, surface roughness, and sealing geometry, ensuring reliable performance and long-term safety of electrolyser stacks.
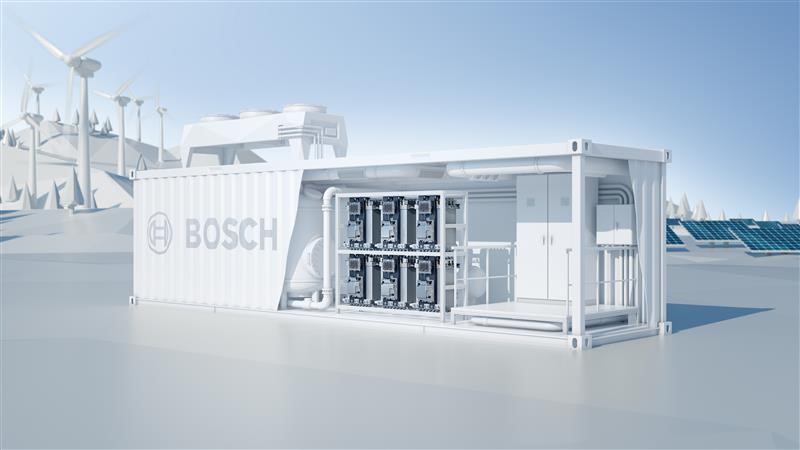
Maria Mione, Bosch Transmission Technology
“Bosch is actively developing the required technologies to produce hydrogen at scale. With the research projects started with M2i, University of Twente and TU Delft, Bosch will accelerate the green energy transition by providing highly efficient and durable green hydrogen electrolyser solutions.”
Celal Soyarslan, University of Twente
“The design of electrolyser bipolar plates is crucial for achieving efficient conversion to hydrogen. The research at the University of Twente on optimizing the manufacturing process for these geometrically complex titanium plates—focusing on titanium’s complex mechanical behavior—combined with improvements in sealing design, will enable Bosch Transmission Technology to develop competitive electrolyser designs at speed.”
Towards hydrogen production at scale
Through the OptBPP, CorBPP, and OPESED projects, Bosch, TU Delft and University of Twente are addressing key technical and economic challenges in electrolyser technology. These efforts represent a significant step towards enabling efficient, cost-effective, and durable hydrogen production systems. By fostering innovation in design, materials, and manufacturing processes, these projects contribute to a sustainable energy future and bolster the global green energy transition.